Metrics Help You Maintain, Improve Your Safety Program
January 20th, 2021
2 min. read
By David Collingwood, Director of Workers' Compensation Claims & Safety
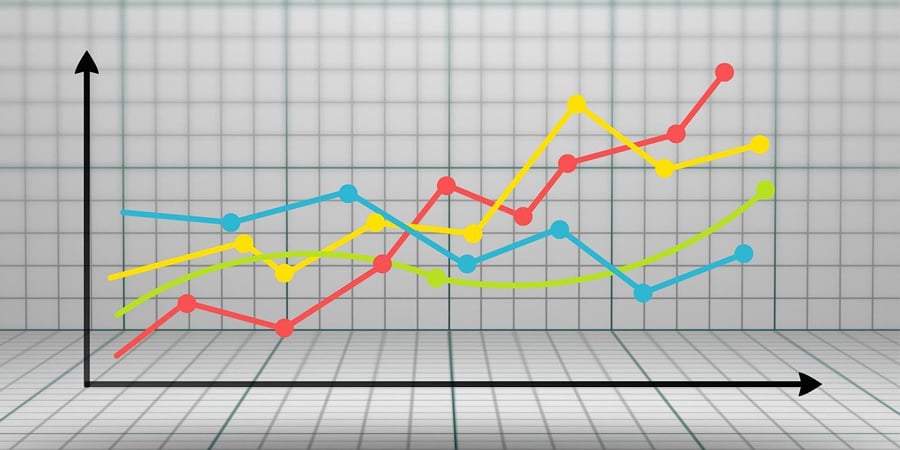
The success of your workplace health and safety program contributes significantly to maintaining a safe workplace, but such programs don’t run on autopilot. According to the Occupational Safety and Health Administration (OSHA), employers should establish a process to continuously monitor program performance and identify any shortcomings and/or opportunities for improvement.
Finding the perfect measurement of success, however, is not as easy as simply documenting the number of injuries that occur in your workplace in a given year.
While measuring the end result is important for many reasons, the data won’t help you identify shortcomings in your program or areas for improvement. For a complete picture of the effectiveness of your safety program, it helps to use a combination of both lagging and leading safety performance indicators.
What are lagging and leading indicators for safety performance?
Lagging indicators are the traditional safety metrics OSHA uses to mark compliance with safety rules, such as OSHA incident rate, lost time case rate, severity rate and DART rate. These rates are quantitative measurements of past safety performance.
Leading indicators, on the other hand, are focused on future safety performance and continuous improvement. They measure your current and ongoing efforts to prevent incidents that could result in injury or illness. These metrics are more qualitative in nature and might include assessments such as tracking safety training, conducting internal safety audits or compiling employee perception surveys.
Using complimentary indicators to provide actionable insights
Individually, lagging and leading indicators show only limited pieces of a puzzle. Together, however, they paint a holistic picture of how well your safety program is working and where you might need to make some changes. Let’s take a look at how some indicators work together to provide actionable insights.
The OSHA incident rate shows the number of work-related injuries per 100 full-time workers during a one-year period. It is calculated by taking the total number of recordable injuries and illnesses in your workplace (available on your OSHA 300A form) in your workplace multiplied by 200,000 (a standardized estimate of the hours worked in a given year by 100 full-time employees), divided by the total number of hours worked by all your employees in a year.
That metric alone doesn’t really tell you much if you have nothing to compare it to, so the Bureau of Labor Statistics (BLS) publishes the average incident rates per industry every year for benchmarking. Different industries have different average rates depending on known risk factors.
Once you know your rate (and how it compares to others in your industry) you can use leading indicators to help you determine why your rate is what it is.
If it is higher than average, you might start by digging into the specific types of injuries recorded (trips and falls, for example) and looking at your employee training for fall prevention. Look for answers to questions like: What kind of training do you offer? How frequently is training held? Who has attended training? Is there a training evaluation to ensure training is understood?
You might also examine if all the recorded injuries qualify as OSHA recordable. Not every injury meets the criteria for a recordable injury and over-reporting can skew your incident rate. On the other hand, under-reporting injuries can also be an indication of a problem in your safety program. Do your supervisors need training to understand how to file incident reports?
Not only can you compare your rate to other companies for insight, but you can also compare your own rate year-over-year for consistency and areas of improvement. If your rate suddenly goes up or down, that’s an indication that you need to do some investigating.
Even if your lagging indicators have remained the same for years, combining them with leading indicators like employee surveys and internal audits will help you document what you are doing to keep your safety performance standards stable.
Looking for tools to help with indicators?
New safety apps and management software are introduced to the market regularly, and many of them include automatic calculations for both lagging and leading indicators.
Check out our latest whitepaper Modern Workplace: Using Technology to Ensure OSHA Compliance and Manage Safety Programs to learn more.
David Collingwood, Director of Workers' Compensation Claims & Safety
In his role at McClone, David is responsible for overseeing two key service areas—workers’ compensation claims advocacy, and safety and loss control. With more than 32 years of leadership experience in carrier work comp claims management, David has worked closely with clients in a variety of industries—construction, manufacturing, healthcare, hospitality, etc.—to help them understand work comp claims processes and mitigate claims. Company safety practices and procedures are key to reducing claims, and David uses his knowledge of state statutes, case law and complex claims to help clients identify risks, increase safety awareness and maximize carrier resources. Prior to joining McClone in 2020, David most recently worked for SECURA Insurance Company. He holds a bachelor’s degree in economics from Illinois State University and served on the board for the Wisconsin Claims Council as well as an insurance liaison on the Wisconsin Workers’ Compensation Advisory Council. David is also actively involved in the Menasha, Wis., community and he currently serves as Vice President of the congregation for Trinity Lutheran Church.
Topics: